精密测量:支撑高端装备制造质量的基石
2021-01-19 12:26:00 我国装备制造要由中低端向中高端迈进,首先要解决制造质量问题,其核心关键是解决超精密测量能力问题。只有解决整体测量能力问题,才能从根本上解决高端装备制造质量问题。
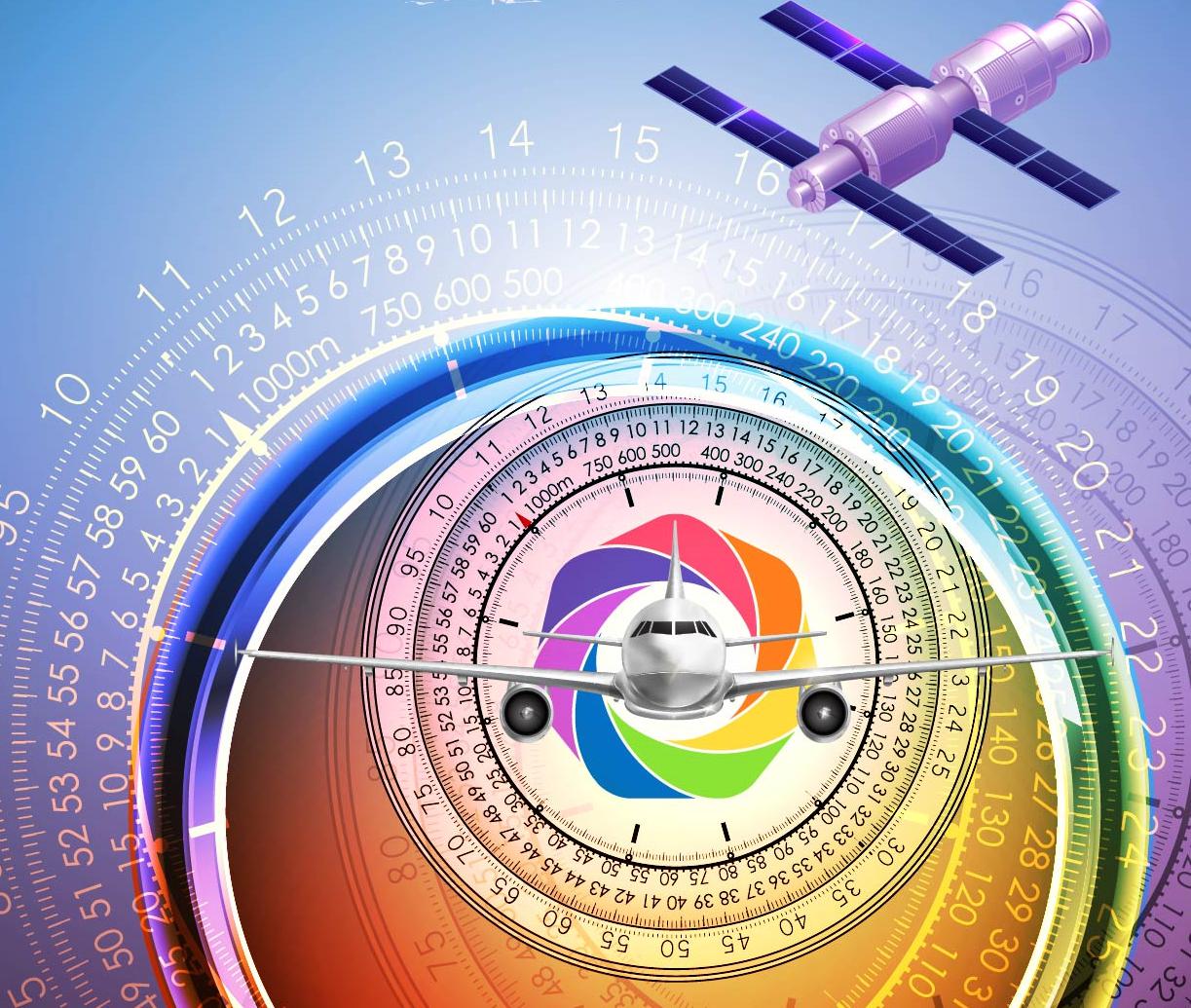
高端装备最本质的特征是高质量。高质量的内涵包括高性能、高可靠性和高稳定性。如果说装备制造业是制造业的脊梁,那么高端装备制造业就是这个脊梁中的精髓。高质量的高端装备制造业可以牵动整个装备制造业和整个制造业高质量发展。因此,高端装备制造业是大国必争的战略制高点,而不断提升高端装备制造的质量水平则是实现这一战略的重中之重。
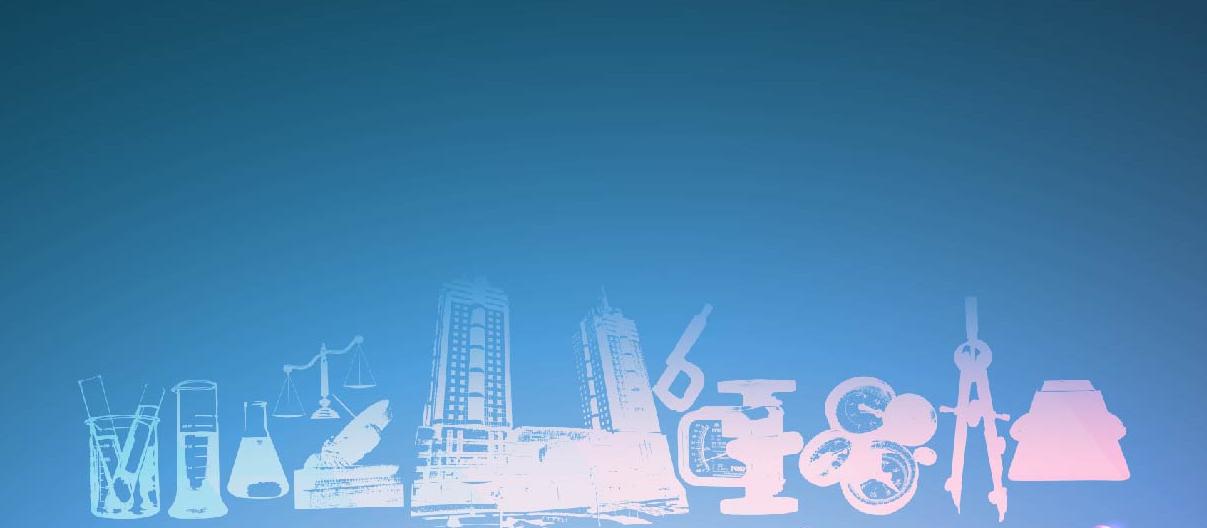
提升高端装备制造质量面临的测量手段挑战
目前,支撑产品制造质量的测量手段可分为三个部分。一是具有测量能力,但这部分测量主要是一种由局部代替整体的测量。例如,在图纸上标注圆柱类零件形状的时候,考虑到现有的测量手段,一般只标注一个截面的圆度,再标注一个竖线的直线度。实际上,这样的测量漏掉了绝大部分有用的信息。二是只具备部分测量能力。例如,在平板显示器生产线上,通常是从6块或8块平板显示器中抽出一块来测量,而且是只在平板显示器上选择几个点测量。这是在抽检的基础上进行局部代替整体的测量方式,测量数据远不能反映平板显示器的制造质量,所以良品率很难控制。三是根本没有测量能力,在图纸上也不标注了。这样的测量能力无法支撑我国高端装备制造,更无法支撑高端装备制造质量的提升。
鉴于上述情况,我国要提升高端装备制造质量将面临三个主要挑战。一是国家测量体系不完整,特别是工业测量体系极其薄弱。二是测量仪器体系呈碎片化,无法满足整体测量能力建设的需求。三是对“精密测量是支撑制造质量的基石”这一基础性和决定性作用的认识严重不足。
国家测量体系可大致分为国家计量体系和工业测量体系两部分,核心任务之一是保证庞大的工业测量数据准确可靠。但是,在这个层面上,我国存在十分严重的量值传递体系不完整问题。以几何量为例,德国建有123种国家计量标准(装置),我国只有80种。国家的计量基标准都由国家计量院建立与管理,标准量值须逐级向下传递。首先传递到大区一级,再传递到省一级,再传递到市一级及县一级,最后传递到工厂计量室。由于受技术能力、地方财力和人力资源等限制,不可能健全与国家计量院计量标准数量对应的计量标准,所以每一级计量机构在建立相应级别的计量标准时,都会减少一些计量标准。这样的计量体系无法支撑我国高端装备制造业所需要的庞大工业测量体系的正常运行,无法保证工业测量数据的准确可靠。
工业测量手段碎片化,即现有的精密和超精密测量仪器的种类极少,只在一些点上有测量能力,不成体系,无法形成整体测量能力。这可从三个层面分析。一是零件层。我国面向装备制造业的测量方式与测量体系,基本上是学习苏联的相关方式与体系,测量主要是面向零件级的几何参数测量。即使是面向零件级测量,实际上在精密级上我们也测不全。我曾经把国内某工厂的图纸和德国某工厂相同零件的图纸进行对照,发现国内图纸标注的参数大量缺失,主要是我们对这些参数没有能力测量,所以在一些图纸上干脆就不标了。按照这样的图纸和测量手段控制零件在制造过程中的质量是不可能的。二是部件层。因产品千差万别,集成调试所需仪器原理和具体测量方法也各不相同,需要专门定制专用测量仪器,而不能直接采用通用仪器。由于部件层现有的专用测量手段基本上都是碎片化的,不能形成整体测量能力,部件集成质量无法控制。三是整机层。不仅部件装配层需要专用测量仪器,整机测量层也需要大批专用测量仪器,整机装调完成以后对整机性能的测试还需要一批专用测量仪器。整机层的状况与部件层状况类似,但更严重。以超精密光刻机上的一个工作台激光反射镜为例,它有108项尺寸公差和62项形状、位置、方向公差,还有内部应力等技术要求。要完成这样一个零件的超精密测量需要20多种专用超精密测量仪器,这些我们都没有提前布局研制,导致我们至今制造不出来精度合格的产品。
中等精度的光刻机有3万多个光机零件,其中70%是精密和超精密级的,需要600多种专用精密和超精密测量仪器,这些仪器90%是我国没有的。还有200多种超精密测量单元和超精密传感器是我国没有规划的,所以我国做了10年光刻机仍不能用。从目前情况看,因没有解决专用超精密测量仪器问题,我国在较短的时间内做出质量合格的光刻机产品是不可能的。
超精密测量的基础支撑作用
超精密测量对提升高端装备制造质量具有基础支撑作用,并在制造全过程中的质量控制发挥决定性作用。国际测量联合会和国际标准化组织曾经联合制定了一个国家质量保障体系,把标准、计量、合格评定三个方面定位为未来世界经济可持续发展的三大支柱。这是总结了发达国家的发展经验后提升到理论层面的一个重要认识。落实到企业的时候,在标准、计量、合格评定三大要素基础上,还要加上认证认可,这样就形成了工厂可操作的质量保障体系。
要想赶上发达国家的高端装备制造质量,首先应看看发达国家的做法。美国高度重视建模和软件,即通过大量的测量数据积累,挖掘影响产品质量的各种误差源,找出其影响规律与消除方法,构建数学模型并形成软件,并不断评估对质量的改善效果。例如,实验室里的激光干涉仪从5528型升级到5529型时,几乎没有改动任何硬件,而是把新的软件嵌入进去,使仪器测量分辨率提高了一个数量级,价格提升了1倍。相比之下,德国人更注重硬技术,靠深度挖掘机器性能来提升质量,而日本人则更强调工匠精神。尽管各国的侧重点不一样,但都是以大量精准测量数据的积累和数据处理为基础的。我国的很多企业家和工程技术人员通常有一个错误认识,就是质量是靠先进的制造装备来保障的。从发达国家高端装备制造发展历程可以知道,只有先进的制造装备是不行的,特别是发展到超精密制造阶段,测量不出来就制造不出来。因此,我们应认识到:只有通过精确测量,才能精确找到产品质量不合格出现在哪里;只有对测量数据进行大量积累和深度分析,才能发现不合格的根源;只有全面精准地消除了产生误差的根源,才能最终提升高端装备制造质量。
发展机遇和方向
对我国而言,优势可能是工业大数据。我国拥有几乎世界上各发达国家的工业母机,不断地积累着大量与制造质量有关的数据。在掌握和深度分析这些数据的基础上,如果我们虚心地学习美国的软件技术、德国的机器硬技术和日本的工匠精神,加上充分的测量能力提升,使后续的测量数据得到高质量延续和积累,这会产生一个后发的综合优势。这个综合优势有利于全面精准地发现各种误差产生的根源、消除各种误差源,扎扎实实地达到提升制造质量的目的。我们必须在以下几个方面形成后发优势。
第一,不断提升全民族的质量意识。我们必须学习德国人,深刻反思我们产品质量不高的根源,关键是要深刻认识到“没有精密的测量,就没有精密的产品”。在此基础上,充分发挥我国具有庞大的测量和仪器技术队伍这一人力资源优势,结合新技术革命与产业变革机遇,形成后发优势。高端装备是工业母机制作出来的。为保证高端装备制造精度,工业母机的精度要比高端装备的精度高一个数量级。工业母机的精度靠超精密测量仪器来保证。超精密测量仪器的精度要比工作母机高出一个数量级,这样才能保证工业母机的精度。因此:从精度的角度看,超精密测量仪器是高端中的高端;从基础支撑的角度看,超精密测量仪器是基础中的基础。我们要充分认识到超精密测量仪器的精度引领作用和基础支撑作用。没有测量精度和整体测量能力这个基础,所有制造精度和制造质量都是空谈。
第二,尽快建立起新一代计量体系与工业测量体系。2018年世界计量大会做出了一个具有深远历史意义的决议,即国际单位制中的7个基本单位均采用基于物理常数的新定义。这意味着我们遇到了一个千载难逢的发展机遇。现在的标准计量量值传递体系,中间经历了一个很长的传递环节,等这个标准计量量值传到车间时,有价值的计量量值已经所剩无几了,再加上车间的测量手段的碎片化,这样的测量体系不可能支撑高质量产品的生产。7个基本物理量都采用物理常数重新定义以后,从理论上讲,这个标准计量量值传递体系的中间环节都可以不需要了。只要满足定义条件,任何部门在任何地点、任何时间都可以把基本量复现出来,不用再按照原来逐级溯源的体系去溯源了。它带来的最有价值的东西就是量值传递体系扁平化。从这个意义上看,我们和发达国家处于同一个起点,我们如果能抓住这一难得的历史机遇,就可以率先建立起最简洁高效的国家计量体系和国家工业测量体系。
第三,加快测量体系数字化进程。数字化是工业4.0的基础,是网络化制造和智能化制造的前提。一个成功案例是西门子公司。西门子公司通过大力发展软件来加快数字化进程,大量抛售硬件公司,如汽车、家电、照明等领域的公司,然后收购其他软件公司。2014年,西门子建立了数字化工厂集团,向数字化工业迈进,然后又大力推广数字孪生技术。这两件事做完以后,它的产品制造周期由原来的18个月降低到8个月,制造成本降低到原来的1/3,产品质量全面提升。
第四,加快工厂工业物联网建设。根据我国网络技术的发展状况,企业面向智能制造的网络化建设可以有两种方式:一是把外网和工厂的内网结合起来;二是直接以5G为工业物联网平台。特别是处于改造升级阶段的企业,没有必要重新布光纤网,可以直接用5G建工厂的物联网平台。
第五,对数字化和网络化已经有一定基础的工厂应及时发展智能化。德国企业的发展方式是循序渐进,即先发展数字化,再发展网络化,最后发展智能化。对我国发展状况而言,应该发挥后发优势,三个阶段的工作并行推进,即全力发展数字化,对必要且成熟的工厂或车间同步发展网络化,同时,依据人工智能技术发展的成熟度,逐步且及时地开展制造过程的智能化。
要尽快提升我国高端装备制造质量,遇到的最大的瓶颈是基础不扎实,而最大的、最根本的基础短板是没有形成整体测量能力。我国要完成高端装备制造质量提升这一伟大历史使命,必须尽快补齐精密测量能力,追平超精密测量能力,同时,充分发挥后发优势,确保在完整精度阶段最后胜出。
谭久彬,中国工程院院士,哈尔滨工业大学精密仪器工程研究院院长,兼任国家计量战略专家咨询委员会副主任、中国仪器仪表学会副理事长、国际测量与仪器委员会(ICMI)常务委员等。
文/谭久彬
本文来自《张江科技评论》